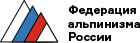
Правда и мифы о карабинах
АВТОР - Андрей Васильев
член комиссии по безопасности UIAA, ведущий эксперт компании VENTO
Много вопросов возникает о том, как производится то или иное снаряжение. «Герои» этой статьи — карабины — наиболее массовый продукт, с одной стороны, и продукт, вызывающий наибольшее число вопросов, — с другой. При всей простоте карабина как изделия о нем можно говорить очень много, и все равно многое останется за рамками обсуждения.
Немного истории
Сам термин «карабин» пришел к нам примерно из VII века как название устройства, которым прикрепляли одноименное оружие к плечевому ремню. Первое устройство, близкое к тому, чем мы пользуемся сейчас, было запатентовано в США в 1868 году. Долгое время карабины были стальными и без муфты. Муфтованные карабины стали массово применяться всего 30–40 лет назад. Наличие муфты значительно повышает безопасность изделия, предотвращая его случайное открытие.
Карабины из дюрали и титана появились значительно позже.В чем-то «развитие» карабина во времени совпадает с развитием компьютерных и других высоких технологий. Сейчас мы наблюдаем «пик инженерной мысли».
Классификация, сертификация, надежность
Можно привести массу вариантов классификации карабинов: по использованному материалу, по способу штамповки (ковки), по типу карабина (B, D, H, K, Q, X; с муфтой / без муфты), по типу муфты, типу открытия и прочим параметрам, подробное описание которых претендует на целый цикл статей.
При этом все карабины конструктивно одинаковы. Они состоят из тела карабина, согнутого из прутка, защелки, которая не только закрывает карабин, но и придает ему основную прочность (открытый карабин выдерживает нагрузку 7–10 kN, закрытый — 20–50 kN), и муфты (исключая немуфтованные). Надо отметить, что сама муфта никак не влияет на нагрузки, которые карабин выдерживает, а лишь исключает открытие защелки.
Стандарты регламентируют три испытания карабина на прочность: вдоль основной оси (в зависимости от типа и стандарта прочность от 15 kN), вдоль основной оси с открытой защелкой (прочность от 5 kN), поперек основной оси (от 7 kN).
Основные стандарты — ГОСТ-Р ЕН362/2008 (ЕТС, промышленный), EN362 (промышленный), EN12275 (спортивный), UIAA121 (дополнительное к EN12275 требование кзащелке муфтованного карабина).
Большинство из нас считают карабин безусловно надежным звеном страховочной цепи. Однако это не так. В обычных условиях восхождения или при проведении спасработ
подручными средствами в страховочной цепи в зависимости от ситуации могут возникать нагрузки, превышающие 10 kN, и, следовательно, единственно безопасным нагружением карабина является нагружение вдоль основной оси при закрытой защелке. При этом реальных ситуаций «нештатной» нагрузки на карабин существует довольно много. В некоторых случаях прочность карабина значительно ниже и может опускаться до 2–3 kN.
Технология производства карабинов
Основой для карабина является дюралевый или стальной пруток диаметром, как правило, 10 мм. Фабрики закупают такой пруток в буквальном смысле вагонами. Далее пруток режется на заготовки длиной 15–20 см, которые поступают в гибочный автомат, где заготовке придается первоначальная форма. Затем следует операция, придающая ей индивидуальность — это горячая ковка (горячая штамповка). То есть заготовка разогревается и далее попадает под пресс. На этот момент она получает ту самую изящную форму, которую задумал дизайнер, а также ребра жесткости и прочее.
Некоторые фирмы «выштамповывают» название компании-производителя, карабина, нагрузки. Ряд производителей указывают на уникальность производства именно их карабинов. Например: «Только мы производим кованые карабины» или «Наши карабины произведены методом горячей штамповки, и только на наших карабинах рельефно нанесено название нашей фирмы». На самом деле, большинство карабинов проходят этап горячей ковки, именно поэтому они имеют не скучно круглое сечение, а различное, с ребрами жесткости и пр. Стоит отметить, что стальные карабины и очень простые дюралевые (с круглым сечением) горячей ковке не подвергаются.
После остывания заготовка попадает еще под один пресс, где с нее удаляются излишки металла (облой), вытекшие при горячей ковке. Далее она подвергается галтовке — процессу, при котором с нее удаляются мелкие заусенцы и производится шлифовка.
Затем на стальную заготовку наносится антикоррозийное покрытие (оно же и окраска карабина).
В случае стальных карабинов это цинк, в случае дюралевых карабинов — анодирование. На этом этапе мы получаем заготовку тела карабина. После, или позже, наносится недостающая маркировка, такая как логотипы производителя, название, артикул, нагрузки и т. д. Отдельно фрезеруется, гнется и т. д. защелка, изготавливается муфта . После этих операций заготовки поступают на сборку. Сборка — процесс на 90% ручной. И именно на этом этапе происходит первичный отсев брака.
Гибка и горячая ковка карабина
Тестирование и контроль качества
Можно выделить два вида тестирования.
Выборочный контроль. Из партии отбирается некоторое количество образцов и происходит контроль прочности по трем осям (до разрушения). Также производится контроль жесткости материала и устойчивости к агрессивной среде («солевая пещера»).
Индивидуальное тестирование. На завершающем этапе производства к карабину прикладывается нагрузка 8–10 kN. Такая нагрузка не разрушает и не деформирует качественное изделие, но является разрушающей для изделий, имеющих внутренние дефекты. Если внимательно посмотреть на новый карабин, то на нем можно заметить небольшие вмятины такого тестирования. Здесь стоит упомянуть еще один маркетинговый ход отдельных производителей. Некоторые из них заявляют: «Только наши карабины тестируются индивидуально!». На самом деле это не так: практически все производители выполняют эту операцию. Скорее, плохо, если этого не делается. Еще раз хочу обратить внимание, что индивидуальное тестирование оставляет на карабине следы, и опытному глазу нетрудно определить, тестировался ли данный образец.
Борьба за вес
Последние годы у производителей наметилась тенденция к минимизации веса снаряжения. В частности, ведется негласная борьба за самый легкий в мире карабин. Нельзя сказать, что это плохо. Но путей снижения веса всего три:
1. Уменьшение размера карабина.
В пределе это приводит к неудобству пользования им.
2. Создание «плоских» карабинов.
Т. е. создание такой формы карабина, при которой он имеет в нужных местах ребра жесткости и выдерживает три обязательных нагрузочных теста. НО! При нагружении карабина в другой плоскости он может выдерживать очень низкую нагрузку. Мне, например, приходилось видеть карабин, согнутый под 90° при неудачном расположении на перегибе.
3. Подбор сплава.
Практически все карабины производятся из алюминиевого сплава 7075. Если подобрать другой, более легкий, прочный сплав, можно «выиграть» несколько граммов. Но этот путь более дорогой, и мало кто из производителей идет им.
Здесь нельзя не вспомнить легендарные отечественные титановые карабины «Ирбис», производимые до 1991 года на НПО им. Лавочкина. В свое время они были исключительно популярны, да и сейчас многие считают эти карабины лучшими. Действительно, в то время это была уникальная альтернатива тяжелым стальным карабинам, они были прочные и удобные. Но если сравнивать их с современными дюралевыми, то они, увы, проигрывают как по весовым характеристикам (титан тяжелее алюминия), так и по эксплуатационным (не самая удачная форма карабина, имеющая очень маленький внутренний объем).
«Изобретение велосипеда»
Казалось бы, что может быть проще, чем карабин: скоба, защелка, муфта. А уж защелка — она и есть защелка. Но оказалось, что поле для инженерной мысли огромно. Появилась муфта, потом появились разные варианты автоматической муфты, потом оказалось, что при лазании по ледопадам вода заливает карабин и он плохо открывается/закрывается — и появилась проволочная защелка, появилась система keylock и ее аналоги. Нет предела творчеству, и каждый год возникают новые интересные идеи: магнитная защелка, защелка, работающая в две стороны, и т. д. Думаю, что нас ждет еще немало интересного в области «карабиностроения»...
В завершение статьи - ответы на некоторые типичные вопросы о производстве карабинов:
«Где производятся карабины?»
Карабины производят очень многие фирмы. Про некоторые из них в России никогда не слышали. И подавляющее большинство фирм, даже самых известных, производят карабины (как, впрочем, и другую продукцию) не на собственном производстве, а на сторонних производственных площадках компаний, занимающихся OEM бизнесом. Примерно 90 % всех карабинов сделаны на Тайване. Крупный OEM-завод расположен в Италии. Безусловно, ряд фирм имеет свои собственные производства, но даже это не означает, что 100 % их карабинов производится именно там.
«Если карабины произведены на Тайване, значит, они не качественные».
Система контроля качества описана выше, и она полностью устраивает ведущие мировые бренды, равно как и сертификационные лаборатории CE, а также UIAA. Не говоря уже о том, что любая фирма проводит дополнительный входной контроль продукции, поступающей на склад.
«Все равно карабины фирмы № 1 лучше карабинов фирмы № 2, даже если они делаются на одном заводе».
Безусловно, трудно «победить» приверженность тому или иному бренду, цвету, размеру. Но, как минимум в рамках одного завода, различие между карабинами разных брендов — в одном ударе штампа, том, который придает заготовке конкретную форму.
Источник: журнал "Горы"
Фото из архива автора, из открытых источников.
+2
8462
Результаты поиска
- Определены победители Чемпионата России 2015 по ледолазанию
- Чемпионат России, технический класс, Каравшин
- НС 2015. Безенги, Джанги-тау
- Андрей Волков: «Альпинизм тренирует в тебе человека»
- Скоростной забег на пик Черского. Открыта регистрация
- Определены победители Чемпионата России 2015 по ледолазанию